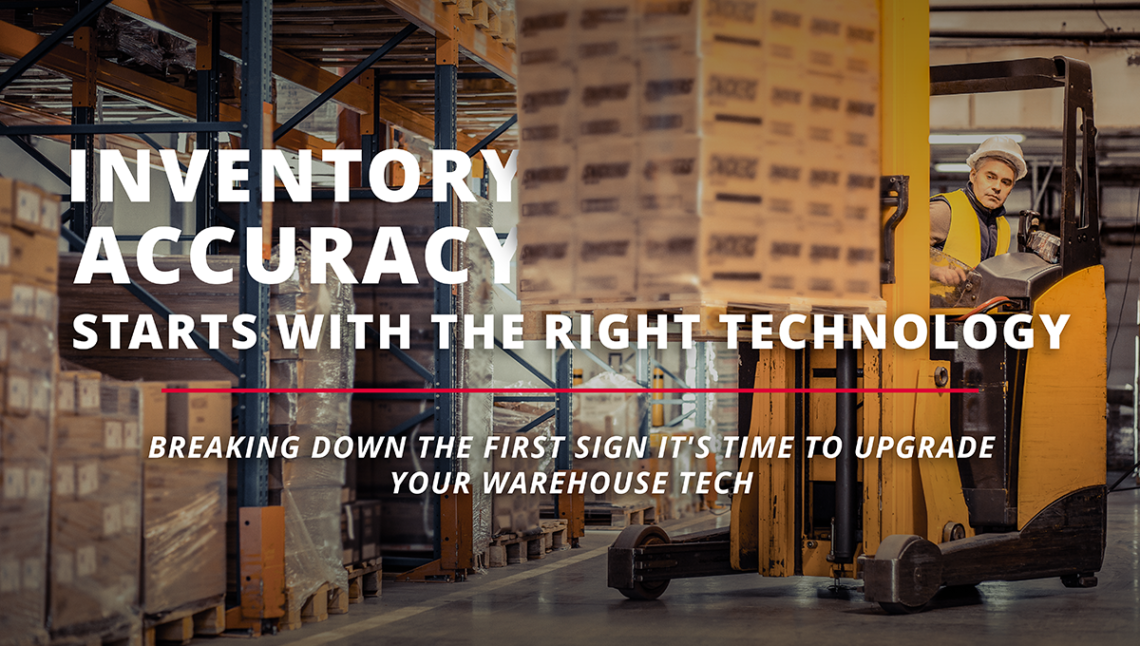
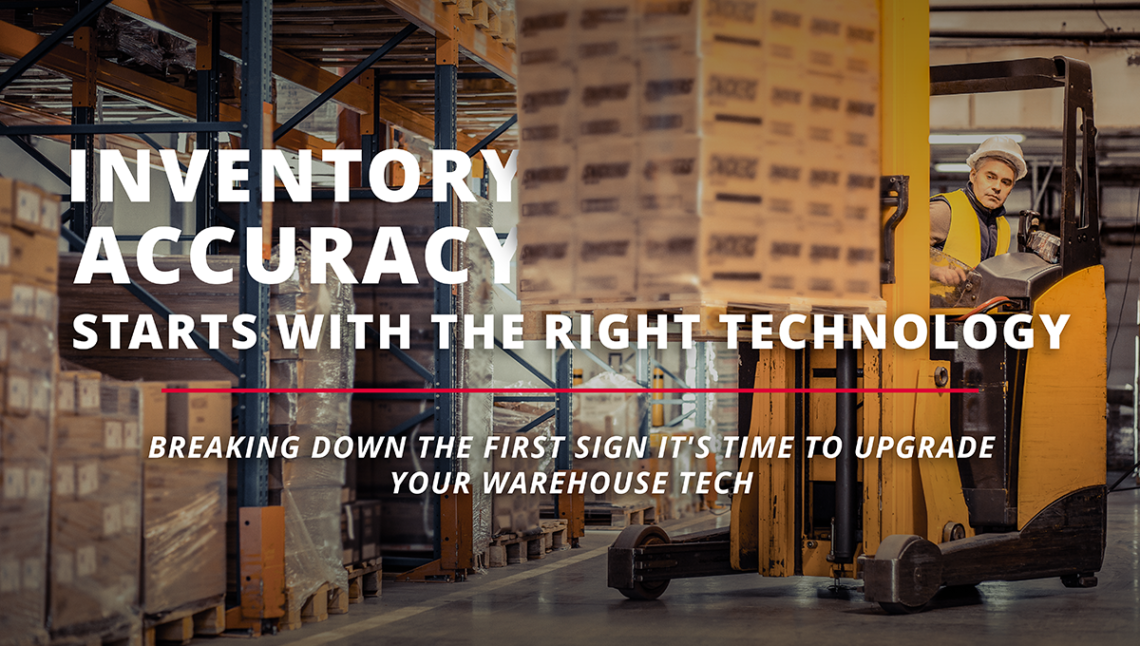
Running a warehouse can be challenging, especially when errors keep popping up. Your technology might be outdated if you’re dealing with misplaced products, incorrect shipments, or mismatched inventory. These problems don’t just slow you down—they can cost you money, frustrate customers, and cause significant delays. At IntegraServ, we help businesses upgrade their warehouse technology to reduce mistakes and keep things running smoothly.
The Problem: Old Tech Causes Warehouse Errors
If your team still enters data by hand or uses outdated barcode scanners, errors are bound to happen. Small mistakes—like typing the wrong number or scanning the wrong product—can throw off your entire inventory. This leads to incorrect stock levels, wrong shipments, and wasted time fixing problems.
Another issue is weak Wi-Fi in the warehouse. Poor connectivity can cause delays in real-time inventory tracking, making it harder to know where products are or if orders are correct. If your Wi-Fi is slow or unreliable, it’s time to upgrade.
The Solution: Smarter Warehouse Technology
At IntegraServ, we help businesses move away from error-prone systems and into smarter, more reliable technology that speeds up and simplifies warehouse operations.
1. Improve Wi-Fi for Better Tracking
A strong, reliable Wi-Fi network is essential for keeping everything connected. Your inventory tracking will suffer if your scanners, RFID readers, or mobile computers don’t always work due to poor Wi-Fi. A Wi-Fi site survey helps find weak spots and ensures you have strong coverage across your entire warehouse. With better Wi-Fi, your team can work faster and eliminate warehouse errors.
2. Use Real-Time Inventory Tracking
Checking inventory once in a while isn’t enough anymore. Switching to real-time tracking with RFID technology and cloud-based inventory systems gives you instant updates on stock levels and product locations. With this technology, you can reduce lost items, improve order accuracy, and always have up-to-date inventory data.
RFID is especially helpful because it doesn’t require direct scanning like traditional barcodes. Employees can quickly scan multiple items simultaneously, speeding up the receiving, picking, and shipping process while reducing mistakes.
3. Automate Data Collection
The less manual work your team has to do, the fewer mistakes they’ll make. Mobile computers like Zebra’s MC9400, wearable scanners like the RS6100, and voice-directed picking systems help workers scan and track products more efficiently. These tools guide employees through tasks, ensuring they pick the correct items and keep inventory records accurate.
Why Work with IntegraServ?
At IntegraServ, we know that upgrading your warehouse technology is a big step—but it’s worth it. We help businesses find the best solutions to reduce errors, speed up operations, and improve inventory accuracy. With better tracking, automation, and a strong network, your warehouse can operate more efficiently and keep customers happy.
Don’t let outdated systems slow you down. Contact IntegraServ today to learn how we can help you build a more innovative, error-free warehouse.