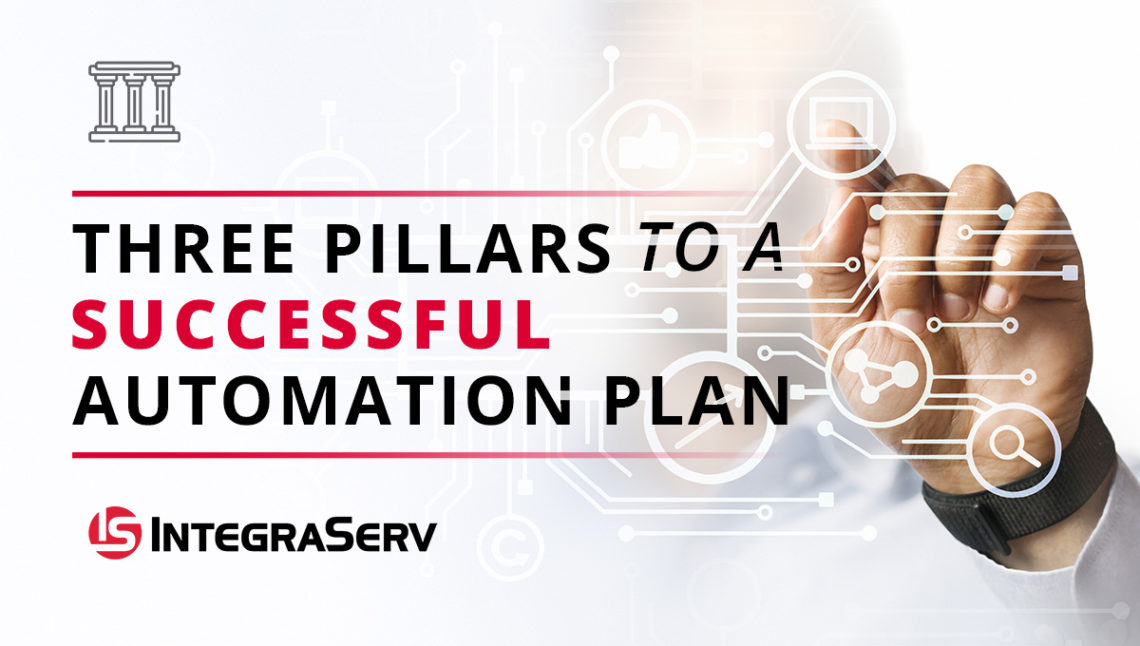
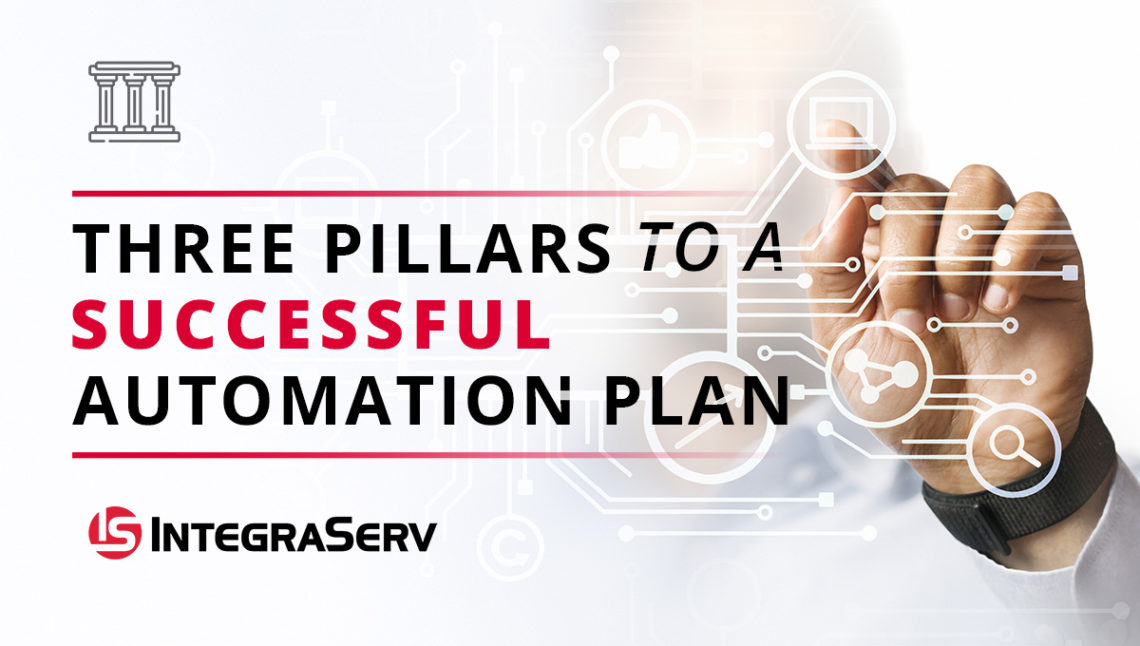
Whether on the production floor or at the loading dock, automation solutions promise to increase profitability without overwhelming workers. Current research shows that 47% of businesses plan to increase automation within the warehouse to combat the ongoing labor shortage. Furthermore, warehouses also struggle to retain qualified labor, with some facilities seeing up to three replacements a year for the same position. While many decision-makers agree wage increases can assist in attracting talent, automation plans aim at retaining workers long-term. About 51% of executives believe automation can boost employee satisfaction as it:
- Eliminates repetitive manual tasks
- Speeds up workflows with less effort
- Minimizes chances for errors
- Connects teams for less isolation
As you consider implementing an automation plan within your facility, it is important to understand the three crucial building blocks to a successful modernization strategy.
- Selecting Purpose-Built Hardware
Consumer-grade devices often seem favorable since they are easy to use and cheaper than enterprise-grade devices. However, these types of devices tend to break easily in warehouse settings, ultimately increasing operational costs as businesses deal with downtime, replacement costs, and delays. Enterprise handhelds like Zebra’s next-generation mobile computers may seem costly upfront, yet they ultimately reduce expenses by:
- Streamlining multiple tasks through one interface – For example, Zebra’s MC9300 handheld consolidates data capture, push-to-talk communication, and inventory visibility into one Android platform. As a result, there is no need for additional scanners and pen-and-paper tracking.
- Preventing data breaches and leaks – Consumer-grade devices lack the robust security parameters needed to prevent notorious attacks from today’s cybercriminals. Government-grade encryption and two-factor authentication are some of the tools currently used to further protect enterprise-ready hardware.
- Withstanding high-impact environments – Lastly, rugged hardware is designed to survive multiple falls, tumbles, exposure to heat and cold, and high humidity. Consequently, devices are less likely to break during critical workflows.
- Implementing Intelligent Software
Hardware acquisition is only half the battle. By selecting an adaptable software solution, businesses can expand their technology’s functionality, adding different tasks to meet consumer demands without having to deploy new systems. Leading software systems like Savant enhance operations with:
- Actionable insights based on captured data over time.
- Dependable traceability for successful audits
- Standardized data processing for seamless report sharing
- 99% order accuracy with maximized visibility
- Partnering with a Dedicated Support Service
In equal importance to the previous factors, a supportive partner empowers your automation plan by proactively strategizing a response to potential challenges and changes. Between device procurement, software installation, and tech support, a managed service partner strengthens you with:
- Access to leading manufacturers, so you can select a purpose-built device fit for your workflows.
- Assisted deployment and training that lowers adoption rates for faster productivity right out of the box.
- Maximized visibility into maintenance needs and updates to prevent breakdowns and vulnerabilities.
- Managed spare pools to accelerate replacements for less downtime.
- Quicker repairs are conducted by specialized experts for less wait time.
Although custom automation plans will include more foundational aspects, these three factors have proven indispensable across the supply chain. Contact our automation team to evaluate your current systems and see how you can enhance your competitive edge.